DCC and EDC are commonly used in programmable power supplies, but they work in very different ways. Below are 5 key differences you should know. DCC uses direct current to transfer signals between two circuits, whereas EDC transfers signals through the electrostatic discharge that builds up and discharges. In short, DCC relies on a steady flow of electrons, but EDC depends on the buildup and discharge of static electricity.
Understanding DCC and EDC
To understand the difference between DCC and EDC, you first need to know what each acronym stands for. DCC is short for Direct Current Coupling, while EDC refers to Electrostatic Discharge Coupling.
Some key differences to note:
- DCC provides a continuous flow of current, so signals are transmitted immediately. EDC has a buildup and discharge of current, so there is a short delay in transmitting the signal.
- DCC requires a complete circuit to work, meaning the signal path must be connected end-to-end. EDC can transmit signals without a complete circuit since it relies on the discharge of built-up static electricity.
- DCC typically has higher power delivery and lower impedance. EDC usually has lower power and higher impedance due to the capacitive nature of the coupling.
- DCC is more prone to ground loops and noise, while EDC is less susceptible since it is capacitively coupled. However, EDC can be impacted by external electromagnetic interference.
- DCC works for both analogue and digital signals, but EDC is typically only used for high-frequency analogue signals. Digital signals often require a direct current path to transmit data accurately.
Also Read > Difference Between Raster Scan and Random Scan
In summary, while DCC and EDC are both methods for transmitting electronic signals between circuits, they operate on very different principles. The method you choose depends on your specific application and needs.
Pros and Cons of Each System
When choosing between DCC or EDC systems for your model railroad, there are some important pros and cons to consider for each.
- DCC
The biggest benefit of DCC is flexibility. You can run multiple locomotives independently on the same track at different speeds. Want locomotive A crawling while locomotive B zooms by at full speed? No problem with DCC. You also have a wide range of functions available like lights, sound, and more.
However, DCC requires expensive and complicated equipment. You’ll need a command station, boosters, decoders for each loco, and handheld throttles. The initial investment can be quite high. DCC also isn’t ideal for very large layouts since its signal can degrade over long distances.
- EDC
On the other hand, EDC, or “analogue DC”, is simple, inexpensive, and fine for smaller layouts. You just need a basic DC power pack and you’re up and running. EDC is also reliable and easy to troubleshoot since there are fewer components.
The downside is you can only run one locomotive at a time. No independent control or extra functions are available. EDC may feel limiting for those wanting more realism.
In the end, choosing between DCC or EDC comes down to how much complexity and cost you want, the size of your layout, and how many locomotives you need to control independently. Either system can provide hours of enjoyment with your model railroad.
DCC vs EDC
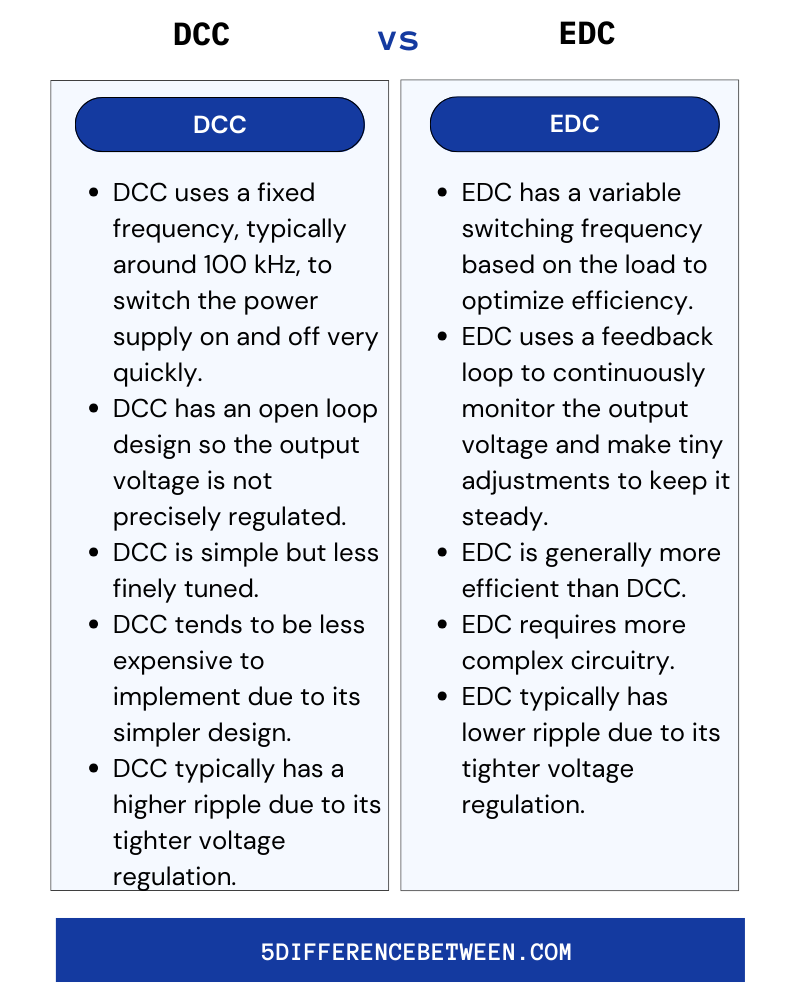
DCC
- DCC uses a fixed frequency, typically around 100 kHz, to switch the power supply on and off very quickly.
- DCC has an open loop design so the output voltage is not precisely regulated.
- DCC is simple but less finely tuned. For many applications, the higher efficiency of EDC leads to lower heat generation and energy usage.
- DCC tends to be less expensive to implement due to its simpler design.
- DCC typically has a higher ripple due to its tighter voltage regulation.
EDC
- EDC has a variable switching frequency based on the load to optimize efficiency.
- EDC uses a feedback loop to continuously monitor the output voltage and make tiny adjustments to keep it steady.
- EDC is generally more efficient than DCC, especially at lower power levels, due to its variable switching frequency and feedback loop.
- EDC requires more complex circuitry to incorporate the feedback loop and variable frequency control.
- EDC typically has lower ripple due to its tighter voltage regulation.
In summary, while DCC and EDC are both used in programmable power supplies, EDC offers significant advantages for many applications due to its higher efficiency, tighter voltage regulation, and lower noise. However, for some basic uses, the lower cost and simplicity of DCC can make it a suitable choice.